Injection molding
Injection molding
Injection Molding in Packaging
Injection molding is a popular method used in the packaging industry to create plastic parts. This process involves injecting molten plastic into a mold to form a specific shape. Once the plastic cools and hardens, it takes the shape of the mold.
How Injection Molding Works
The injection molding process starts with plastic pellets being heated until they melt. This molten plastic is then injected into a mold under high pressure. The mold is a hollow form that shapes the plastic into the desired design. After cooling, the mold opens, and the finished part is ejected.
Advantages of Injection Molding
Injection molding offers several benefits for packaging. It allows for high-volume production, meaning you can create many parts quickly. The process also ensures consistent quality, as each part is identical to the mold. Additionally, it supports complex designs, making it ideal for intricate packaging solutions.
Applications in Packaging
In the packaging industry, injection molding is used to produce a variety of items. These include bottle caps, containers, and custom packaging components. The ability to create detailed and durable parts makes it a preferred choice for many packaging needs.
Materials Used in Injection Molding
Various plastics are used in injection molding for packaging. Common materials include polyethylene (PE), polypropylene (PP), and polystyrene (PS). Each material offers different properties, such as flexibility, strength, and clarity, allowing for tailored packaging solutions.
Conclusion
Injection molding is a crucial technique in the packaging industry. It provides a reliable and efficient way to produce high-quality plastic parts. Understanding this process can help you appreciate the complexity and precision involved in creating everyday packaging items.
Blog Posts with the term: Injection molding
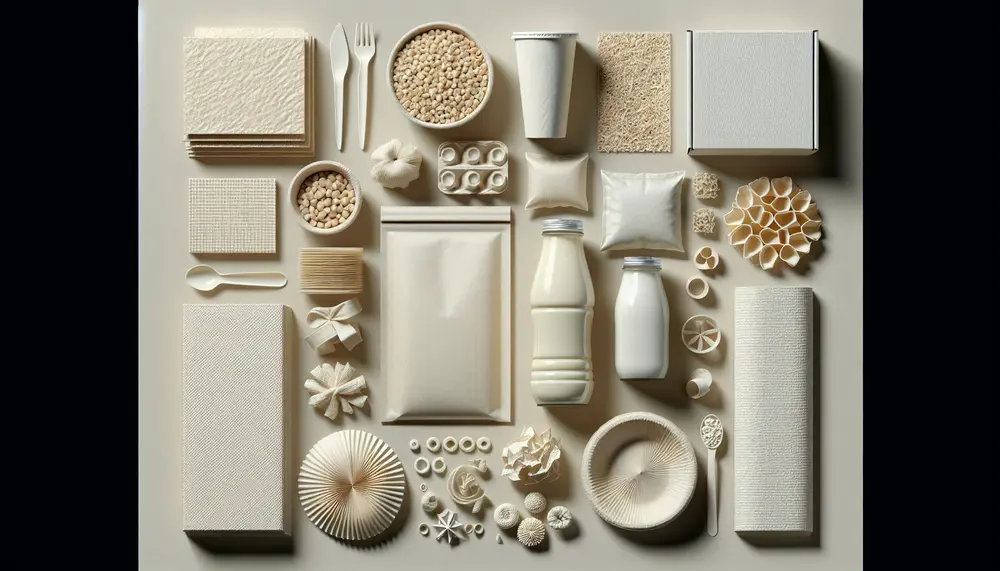
Cornstarch is a biodegradable, eco-friendly alternative to traditional packaging materials, offering similar functionalities with less environmental impact. It's used in various industries for products like containers and bags, reduces reliance on fossil fuels, and supports climate change efforts by emitting...
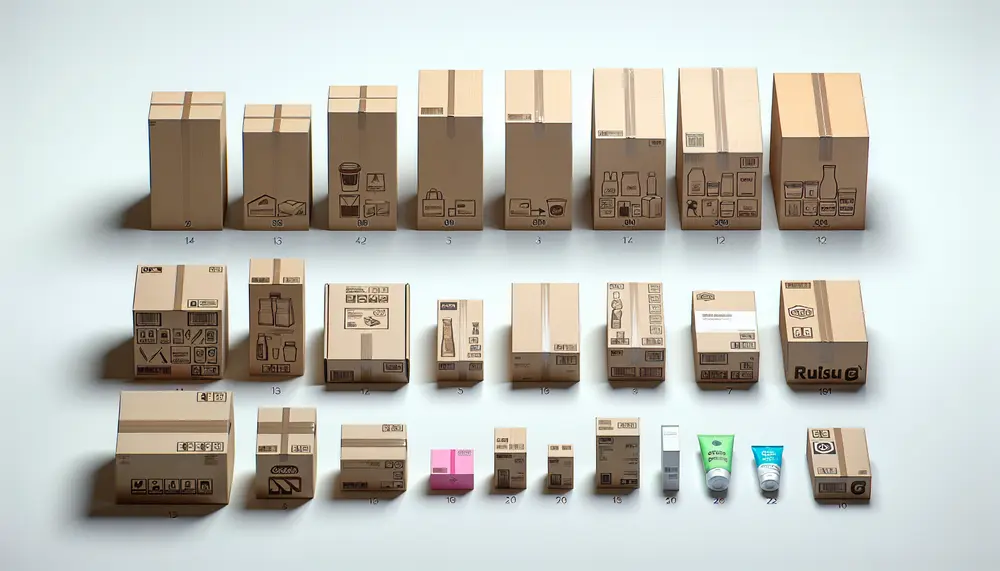
Product packaging is essential for protection, marketing, and providing consumer information; it influences brand perception and purchase decisions through design elements like color schemes. The design process involves research, feedback, prototyping, and technical considerations to ensure functionality and appeal. Choosing packaging...
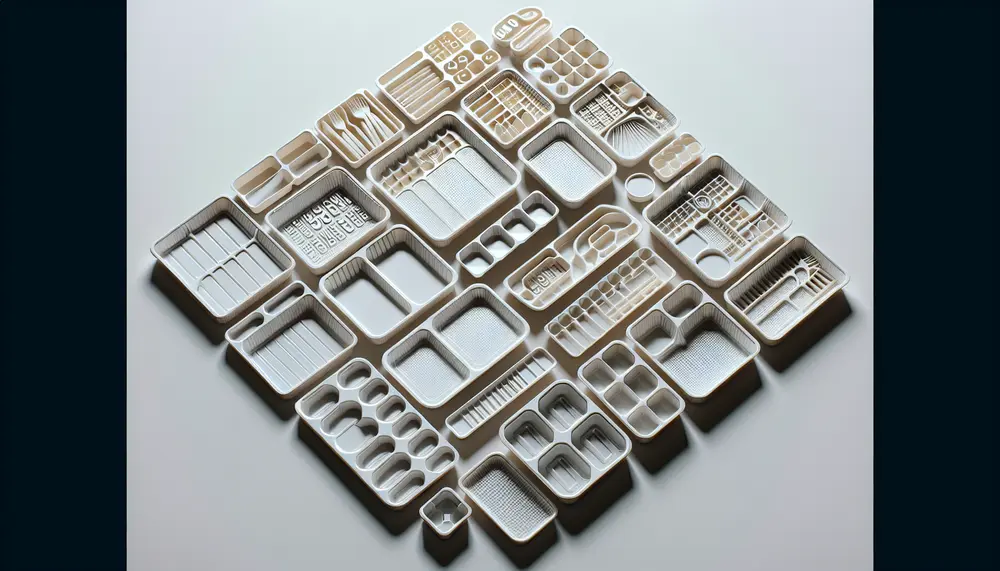
Plastic trays are essential in various industries for their customizable size, shape, and material, offering versatility from warehouse organization to sterilized medical packaging. They come in different designs like compartmentalized or vented ones and have evolved with eco-friendly options to...
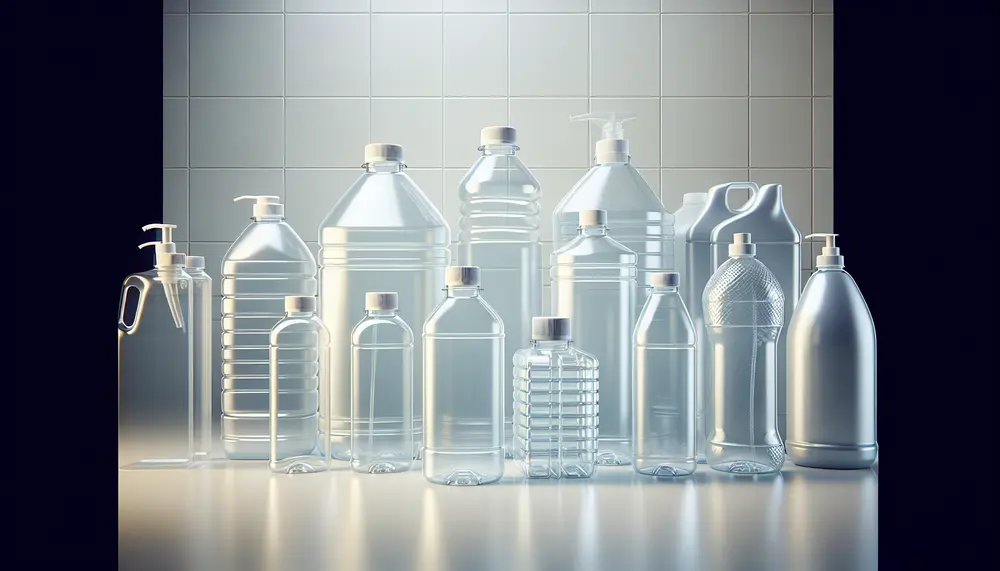
Plastic packaging for cleaning agents is designed to be chemically resistant and secure, with specific plastics chosen based on their interaction with the product's chemicals. Child-safe features like CR closures are essential for preventing accidental access by children. Eco-friendly plastic options...
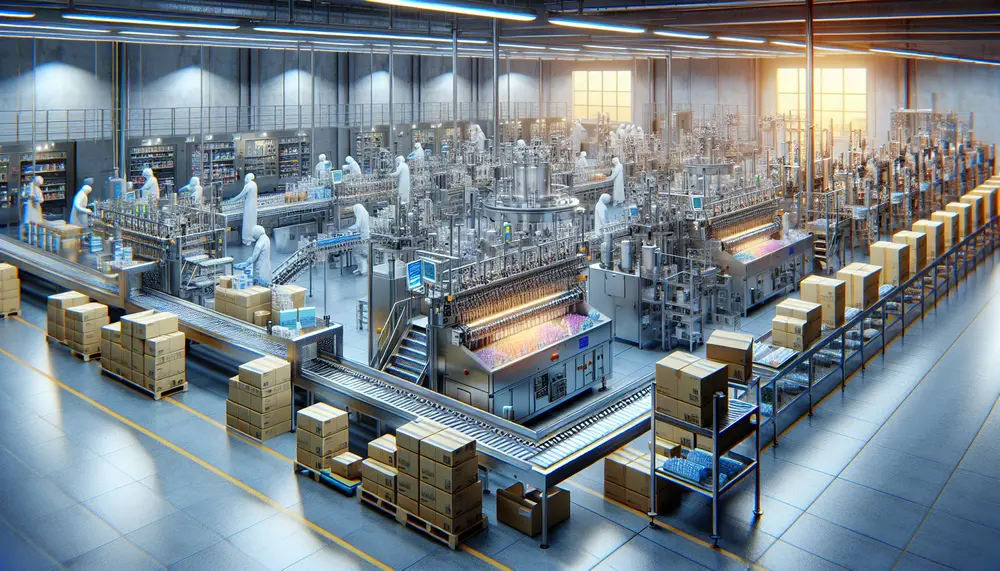
The pharmaceutical packaging value chain is essential for ensuring medications are safely delivered from manufacturers to patients, involving steps like design and development, material selection, manufacturing processes, quality control, distribution logistics, regulatory compliance, and sustainability. Each component plays a crucial...
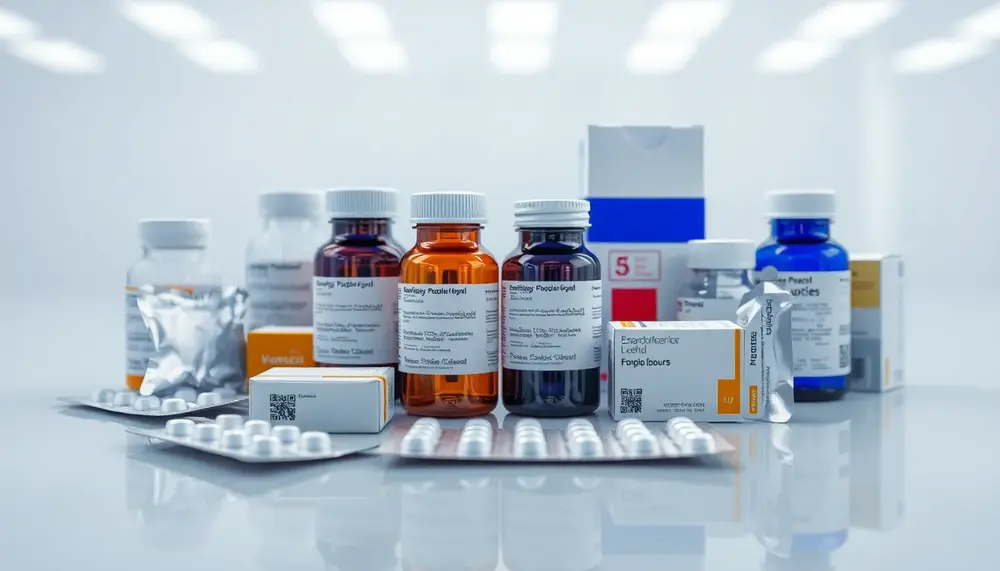
Pharma-grade packaging is a meticulously designed system that ensures the safety, stability, and usability of medications by protecting them from environmental factors, contamination, and degradation while meeting strict regulatory standards. It incorporates advanced materials, user-friendly features like tamper-evident seals, and...